Comment fonctionne IO-Link ?
Les environnements industriels produisent plus de données que jamais. Que ce soit le volume de production, le temps d'arrêt ou les numéros de série, ces informations portent sur les procédures et la productivité.
Many plants rely on this data for tracking purposes but it can also be used for much more:
- Improve operations
- Expand go-to-market strategies
- Rationaliser la maintenance
- Boost uptime
- Increase yield
The trick is to find a way to collect, analyze and display it. Using plug-and-play smart sensors powered by IO-Link can help you take full advantage of the data your plant generates.
Where Did IO-Link Come From?
Within the last decade, the industry has experienced a few big changes:
- To be used in things like robots or attached to hard-to-reach equipment, sensors needed to become smaller as mechanical components were shrinking. This made it difficult to integrate fieldbus interfaces into sensors due to size limitations.
- Manufacturing and automation equipment became more complicated which created the need to gather and control data beyond basic “on/off” or “high/low” capabilities.
- It was becoming more difficult to keep up with the various types of cables used for digital and analog sensors. Each required a different installation configuration and needed to be stocked in case of performance problems.
These factors drove the creation of worldwide IO-Link technology. As a standardized interface, it works in the smallest of devices from any manufacturer around the globe. Furthermore, IO-Link devices can be easily integrated via an IO-Link master to different kind of fieldbus environments or automation systems (more on this below).
What is IO-Link?
IO-Link is a simple, point-to-point communications protocol used, for example, in factory and logistics automation environments to link sensors and actuators to the fieldbus or industrial Ethernet.
This protocol makes sensors "smart." Without it, simple sensors can communicate one parameter: on/off, no object/object present, high/low, etc. With IO-Link, even small sensors can communicate much more data-and translate that data to actual values. Instead of telling you whether a temperature level is "high" or "low," for example, smart sensors utilizing IO-Link can provide current temperature readings.
IO-Link can be compared with USB, which is a famous point-to-point communication protocol used extensively in the enterprise world. It connects computer accessories-monitor, mouse and keyboard-to your computer, for example.
For easy installation, a single cable is run from an IO-Link device (such as a sensor or actuator) to an IO-Link master, which controls communication with devices and links to networks like EtherNet IP or Profinet to share information with the control system. Data is transmitted from the IO-Link master via a high-level fieldbus communications protocol to a PLC or computer. In the enterprise example above, the mouse or keyboard would be the IO-Link device and the computer would be the IO-Link master.
The Value of IO-Link
In addition to facilitating fast, cost-effective communication among devices to reduce downtime, IO-Link offers other benefits as well.
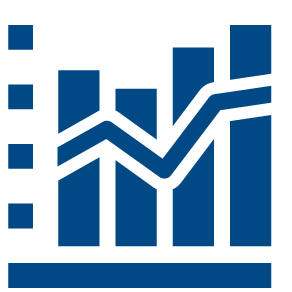
Data Storage
IO-Link masters can store up to 2 KB of the parameters that impact how a sensor or actuator functions. When a device connects to the IO-Link master, the correct parameters are automatically uploaded. This makes things like sensor replacement quick and easy, with no need for manual intervention once the device is installed.
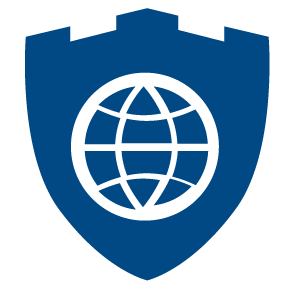
Remote Configuration & Monitoring
Device and sensor parameters can easily be changed remotely as needed, saving valuable time in the manufacturing process to accommodate things like product changeovers (shifting from small bottles to large bottles on a production line, for example). This also makes it easier to reconfigure devices in hard-to-reach locations. Sensor outputs and status alerts can be monitored remotely in real time to help you quickly identify and resolve problems before they cause downtime.
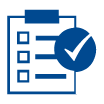
Diagnostic Capabilities
Smart sensors equipped with IO-Link can communicate about their own status via the IO-Link master to the PLC. Before processes come to a halt, you'll know immediately if a sensor needs to be replaced, requires maintenance or is experiencing an error. This gives you the ability to optimize machine maintenance schedules and diagnose problems with a specific sensor without shutting down the entire line or a piece of equipment.
3 Limitations of IO-Link Technology
While IO-Link has the capability to streamline manufacturing processes and save valuable time, it also has a few limitations:
- The cable that runs between the IO-Link device & IO-Link master has a 20 m distance limit
- IO-Link devices can transmit up to 32 bytes per cycle, however, it can’t transmit megabytes of data
- IO-Link is designed for integrated automation applications. If you manage simple standalone applications, you may not see a great benefit from IO-Link
Working with an IO-Link Expert: Belden
With the addition of IO-Link hubs to Belden’s LioN-Power IO-Link System, sensor and actuator connectivity are improved.
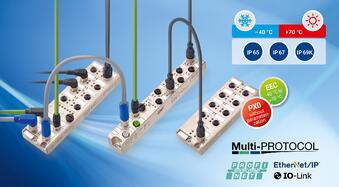
Belden’s system also offers several industry-first features that set it apart when it comes to improving uptime and conserving workforce resources:
- Developed the world’s first IO-Link master with multi-protocol to support both PROFINET & EtherNet/IP (2015)
- M12 hybrid connectors & cables that combine data & power to simplify device needs & lower cost
- The ability to transmit up to 16 A per module (vs 4 A) with the first IO-Link system using M12 L-coding (supports daisy chaining)
- IP65, IP67 & IP69K housing ratings for superior resistance to mechanical stress, shock, vibration, dust & water